The invention of the float glass process
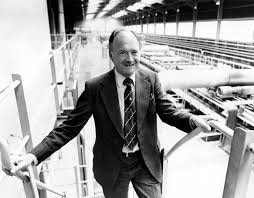
The process called "float glass" for the industrial production of flat glass was introduced in the late XNUMXs.
It was Sir Alastair Pilkington who perfected this manufacturing process: he set himself the goal of obtaining, at lower costs, the glass of the quality necessary to make car windows, mirrors and other uses where the absence of visual aberrations. Until then, the printing method was used, which consisted in making the sheet by casting, extrusion or lamination: the surfaces, consequently, did not have optically parallel faces, giving rise to the characteristic visual aberrations. Parallelism was subsequently obtained through a mechanical polishing operation and this involved a considerable increase in costs.
Why is it called float glass?
The use of the term float, from the English verb “to float” which means “to float”, is due to the fact that, at a certain point in the process, the glass ribbon in formation is found to float on a layer of molten tin.
The stages of production
The merger
The raw materials used are: a vitrifying agent - silica sand (73%), a stabilizer - calcium carbonate (9%), a flux - sodium sulphate (13%). To these components a certain mass of recycled glass is added, in fragments, to reduce the gas consumption of the smelting furnaces.
The raw materials contained in a silos are weighed, mixed and humidified. In this way a vitrifiable mixture is obtained which is conveyed by conveyor belts to the melting furnace, where the temperature reaches 1550 °.
The tin bath
On leaving the furnace, the molten glass is passed over a bath of liquid tin, the “float bath”, at a temperature of about 1.000 ° C.
Glass, which at this temperature is very viscous, does not mix with tin which is fluid, but floats on it forming a flat and smooth surface. The glass is then pulled to become a "ribbon" with parallel faces. Cogwheels (top-rolls) stretch or retract the glass laterally to obtain the desired width and thickness (which can vary from 1,1 to 19 mm).
The annealing
In order for the glass ribbon, made absolutely flat, to be cut into sheets without problems, the annealing phase is necessary: it serves to modify the internal tensions of the glass.
The glass leaves the tin bath at a temperature of about 600 ° C and is deposited on the rollers of a cooling tunnel (about 100 meters long): at 500 ° C the glass strip acquires the properties of a perfectly elastic solid and then it continues to cool under control until it reaches room temperature.
Cutting
The web is ready to be cut into standard glass sheets (3.210 x 6.000 mm) and the longitudinal edges are eliminated. At the end of the line, the slabs are moved with suction cup elevators and positioned vertically on the backs.
The figure below illustrates, from left to right: the feed with raw materials, the melting furnaces, the first cooling on molten tin, the annealing furnace, the cutting of the casting plates and the subsequent loading of the plates onto the media. of transport.
