
COMPANY PROFILE
EUROTECH-WAY has been a leading company in the production of automatic machinery for the glass sector since 1996, but the experience of over 50 years of the Eurotech-Way technical team in the industrial automation sector has an even greater overall impact.
MISSION
We are able to offer advanced, reliable and customized technical solutions, taking care of customer requests and committing ourselves to assisting them at any time.
VISION
Our goal is to make every glazier's life easier.
CERTIFICATES AND ACHIEVEMENTS
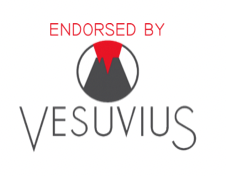
PLANNED EXHIBITIONS 2023
Milan, Italy – 5 / 8 September
ROBOCLEAN
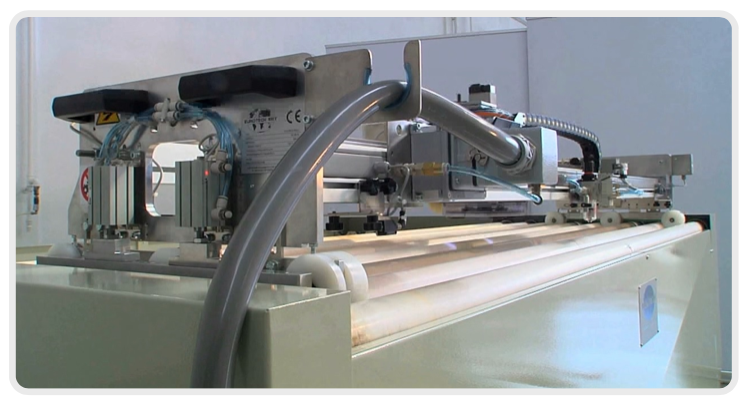
RoboClean is a revolutionary robot capable of automatically removing any type of dirt (lumpy/molten) such as glass, enamel, So2 residues, etc., from the surface of the rollers inside the oven.
This is the only possible way to get the rollers cleaned and polished in a fully automatic way. Its high quality cleaning results are 100% guaranteed and APPROVED by VESUVIUS.
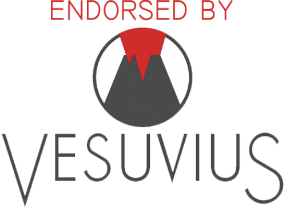
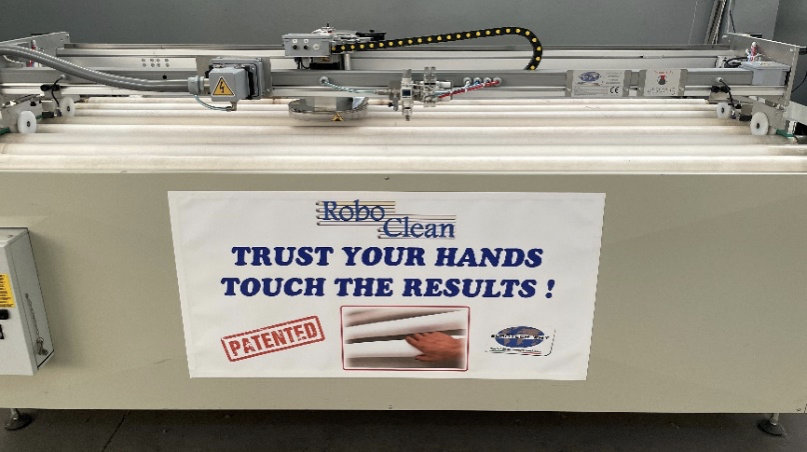
ROBOCLEAN IN ACTION ON ROLLERS
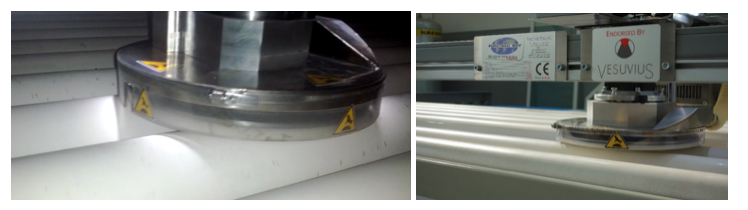
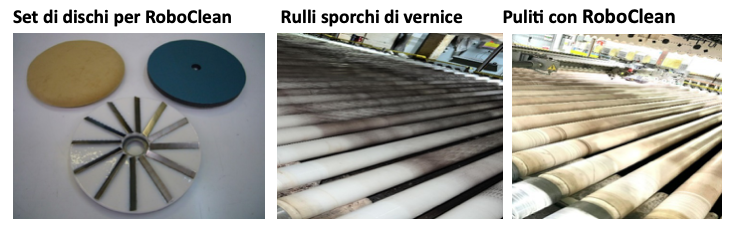
MAIN PERFORMANCES OF ROBOCLEAN
-With RoboClean and the right kits, you'll be able to clean multiple ovens of any type
-With these kits it is possible to change the RoboClean set-up in a very simple and fast way.
-By using RoboClean, you can save manpower, reduce production downtime and avoid the risk of any defects on the glass coming from dirty rollers.
-RoboClean can be equipped with different types of discs, each capable of removing any type of dirt from the surface of the rollers.
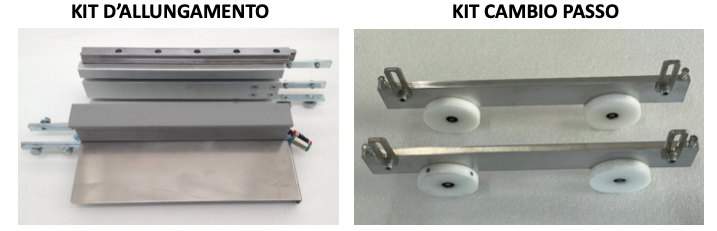
Check out the new release of RoboClean here: https://youtu.be/wC7xrshSdrk
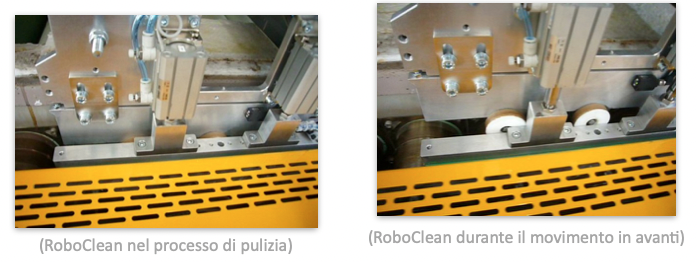
MAIN FEATURES OF ROBOCLEAN
The machine moves forward on the rollers automatically, using the rotational power of the rollers, without requiring any manual intervention or any type of additional drive.
- RoboClean is able to clean the forward and reverse rollers.
- Cleaning head equipped with centesimal micrometric adjustment system, self-levelling at constant pressure.
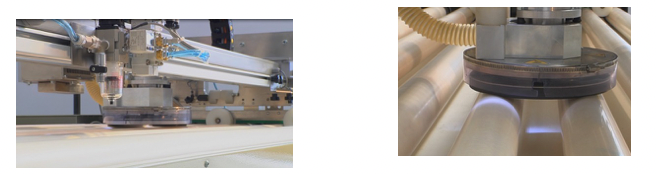
- Cleaning kit complete with 3 discs (Cleaning, Polishing, Dusting) to guarantee maximum cleanliness and brightness to the roller.
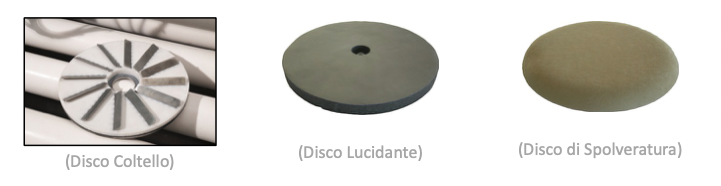
- Given its simplicity of removal and assembly, a simple screwdriver is enough to remove the discs
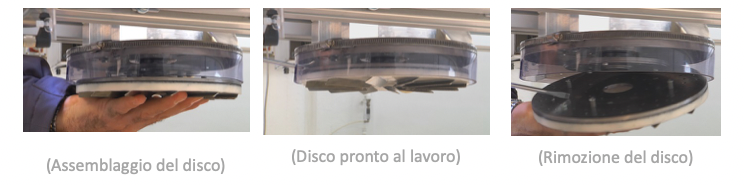
- Suction filter installed on the machine, with clogging signaling system. Any type of fault detected during operation is signaled by the control panel.
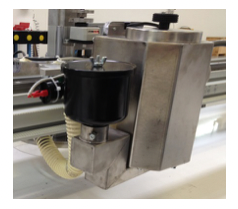
- Application on different ovens with a single machine thanks to extension kits, pitch change kits and management of various recipes stored in the PLC.
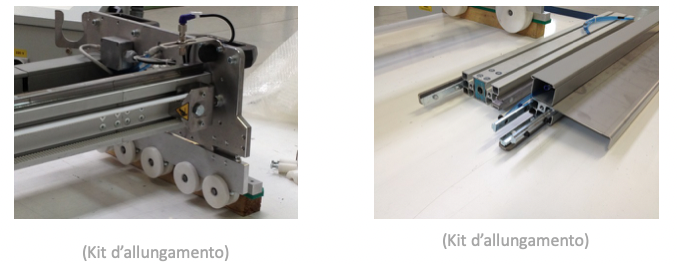
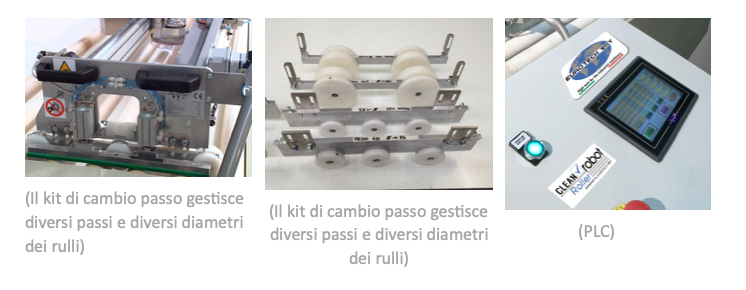
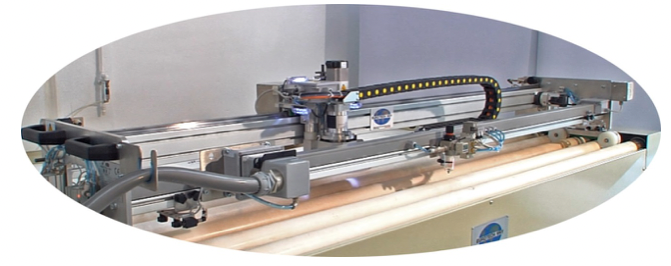
TECHNICAL SPECIFICATIONS
- Power supply: 220 Volts 60Hz – 110 Volts 50Hz
- Installed power: 2,8 Kw
- Pneumatic feed: 6 bars – 10nl/'
THE PERFECT ALLY FOR EVERY GLASSMAKER
- Different ovens can be managed by just one robot, as all operating parameters can be stored in recipes.
- Using this robot, the cleaning times of the rollers are significantly reduced compared to traditional manual systems.
- The glass that comes out of the kiln is of high quality and free from defects that could be caused by the surface of the roller, for the following important reasons:
- Polishing of the surface of the roller in order to reduce its porosity and make the part in contact with the glass shiny, smooth and less sensitive to dust or other residues.
- The complete cleaning process is carried out dry, without using water or chemical additives which in the long run could cause the cracking effect, thus damaging the surface structure of the rollers.
- The uniform, clean and shiny finish of the entire surface of all rollers is 100% guaranteed.
THOUGHTS FROM ROBOCLEAN BUYERS
“I have to say that this is probably the best non-productive machine we have ever purchased. The savings in oven downtime is significant, as no rolls need to be removed and heating back up time is reduced, as the rolls do not have to be sluggishly dried. The manpower requirements for cleaning the rollers are significantly reduced, as it only requires one person to start the cleaning process when RoboClean has been installed in the machine. The quality finish is such that there are no defects on the glass. Even though we have three ovens that this machine can clean, I have to say that even for one oven the return on investment would be very fast if you buy this machine.”
Steve Mayhew
Chief Operating Officer at Village Glass
“We are extremely satisfied with our RoboClean. One of the three ovens we cleaned was extremely dirty, as it took several passes to clean it. Despite this, the robot managed to clean the rollers thoroughly, something I didn't think was possible. A THOUSAND THANKS."
Ivan Martintoni
General Manager at Protemp Glass Inc.
AUTOMATIC SCREEN PRINTING MACHINES
This new series of screen printing machines with mobile bridge technology was developed by the Eurotech-Way team to have more flexible and faster machines with larger free spaces for the operator and to make the transition to production easier and faster, with a very low maintenance and using high quality materials confirmed by our customer.
In fact, during the production changeover, the operator only has to position the spatulas and the screen by hand.
Additionally, each model has a wide minimum and maximum range of glass sizes. In fact, the same model can print from a minimum size of 50x500mm up to a maximum size of 2200x5000mm, without losing its output capacity and simply recalling a specific recipe.
The positions of all other machine parts are stored in a recipe. By recalling it, all the parts of the machine are automatically positioned in the correct position.
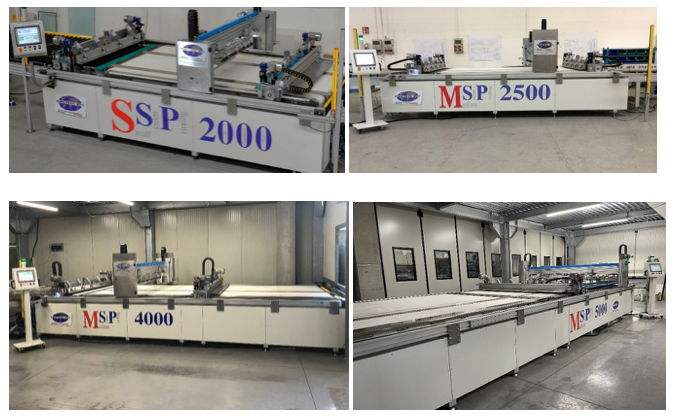
MAIN FEATURES OF THE AUTOMATIC SCREEN PRINTING MACHINE
- PRINTING SYSTEM WITH MOBILE BRIDGE
The mobile bridge printing system is one of the latest innovations, thanks to which the operator has free access to the printing area.
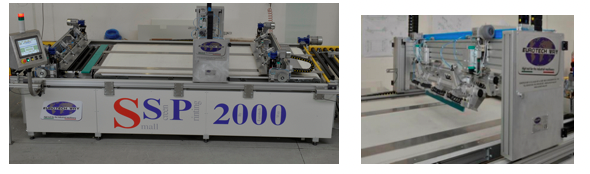
2. TRANSPORT SYSTEM
The transport system can be equipped with belts or bands depending on the size of the glass to be processed.
In the case of a belt conveyor, the glass can be positioned and centered on the closest point and on the most convenient side for the operator, thus facilitating any operation.
Belt conveyor
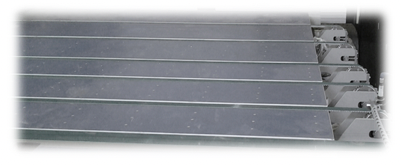
Belt conveyor
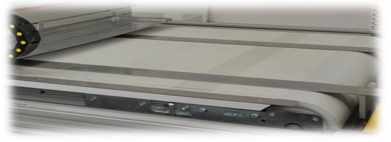
Front stop device and side guides
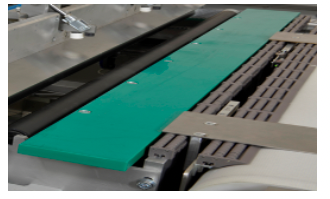
(Automatic adjustment via operator interface based on glass size and thickness)
3. SCREEN SUPPORT UNIT
Screen locking by pneumatic cylinders
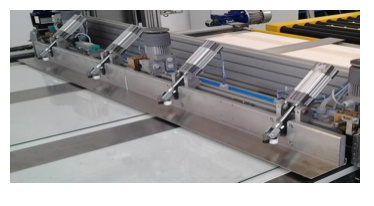
4. OPERATOR INTERFACE
Touch screen panel
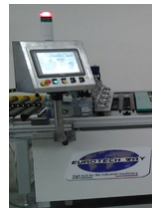
• Automatic screen support system up/down with automatic positioning of the screen height according to the thickness of the glass to be printed.
• Movement out of contact with the compensation system.
• Automatic movement system that compensates for the loss of tension in the mesh over time, guaranteeing equidistance between the scraper and the mesh, thus allowing for a perfect and uniform diffusion of the glaze.
• Each setting is performed by the operator via the Touch-Screen panel, which also allows you to save data, create and recall processing recipes.
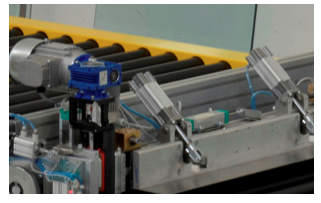
5. DOCTORS
• Automatic adjustment of the pressure of the application blade, based on the thickness of the glass to be enamelled.
• Blocking of the blades by means of pneumatic cylinders.
• Integrated anti-drip system.
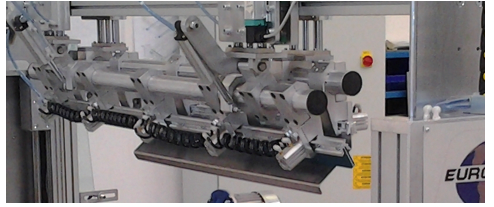
TECHNICAL SPECIFICATIONS
- Glass thickness: from 3 mm to 19 mm
- Maximum printable format: 2200 x 5000 mm
- Minimum printable format: 50 x 500 mm
- Installed power: 12 kWThe
DRYERS
This new series of dryers was developed by the Eurotech-Way team to have dryers with high production, low consumption and minimal maintenance like all Eurotech-Way production machinery.
The heating elements are infrared lamps positioned at the top and bottom of the heating chamber.
The transport system is equipped with ground and polished ceramic rollers with quick release.
All motors and fans are controlled by inverter via PLC and touchscreen.
The temperatures are controlled separately between the upper and lower part of the rollers by means of special thermocouples and self-regulators.
A capillary suction system positioned around the entire perimeter of the heating elements prevents the drying fumes generated by the paints from escaping, thanks to separate adjustments at each suction point.
The cooling system consists of a series of separate high pressure electric fans for the system above and below the glass.
IRD DRYER
The IRD dryer designed and manufactured by Eurotech-Way is a state-of-the-art machine, specially conceived for drying any type of ink or glaze using a high-tech heating system, with special insulating material which allows for a reduction in consumption .
All dryers developed by Eurotech-Way are changeable in trim and can therefore be adapted to customer needs.
The main features of the IRD dryer are as follows:
TRANSPORT AND MOTORIZATION SYSTEM
The transport system consists of ground and polished alumina ceramic rollers.
The rollers are driven by dry mounted bevel gears with quick coupling/release of the roller, controlled by an inverter.
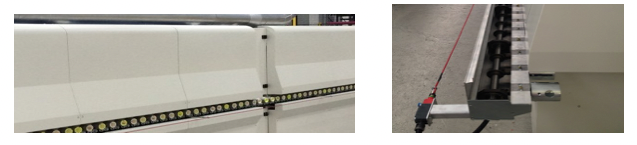
- HEATING ELEMENTS
Supporting structure in painted steel.
Insulation of the heating element sized according to the operating temperature.
Internal coating with AISI 430 reflective heating elements, which amplifies the thermal power of specific equipment.
- HEATING SYSTEM
The heating system consists of resistance heating coils screened up and down between the rollers.
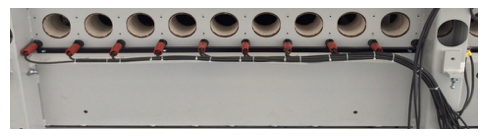
Temperatures are controlled separately on each heating element and between the top and bottom sides of the rolls using special thermocouples and self-regulators.
Each heating element is equipped with a closed-circuit forced hot air convection system for maximum energy saving, consisting of an inverter-controlled fan and a battery of special diffusers.
This system guarantees a perfect distribution of the hot air on the glass panel, controlling the air and the temperature according to the production needs, thus obtaining a thermal balance inside the heating elements.
The thermal insulation of the heating elements consists of high quality insulating material with a thickness of 100 mm, which allows the machine to work at a temperature of 250°, guaranteeing maximum thermal insulation. The internal insulating panels are positioned so as not to create any contact with the external structure, avoiding the normal transfer of heat and thus allowing a natural dissipation of heat towards the outside.
The internal lining of the heating elements that cover the insulation is made of stainless steel sheet which reflects brightness and temperature, to obtain maximum efficiency and heat exchange with consequent energy savings.
A widespread suction system installed along the perimeter of the heating elements avoids any escape of vapors generated by the glaze, having a separate regulation in each suction point.
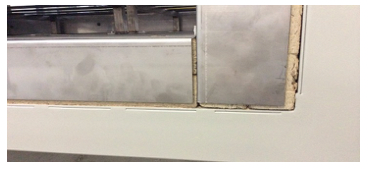
COOLING SYSTEM
The cooling system consists of a series of high-pressure electric fans installed on the above-glass system and the below-glass system. The electric fans inject a considerable mass of air at room temperature into the tunnel, which is then dissipated through special diffusers, cooling the glass.
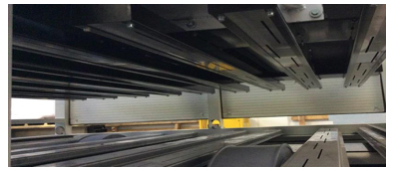
Before being circulated in the tunnel, the air is filtered. The air entering the tunnel is then drawn in by pipes connected to the main fan of the suction stack.
AUTOMATION
- The machine is controlled and managed by a PLC with dedicated software.
All parameters relating to speeds, cycles and temperatures are managed through a touch-screen operator interface, all being controlled by an inverter, allowing the parameters to be saved in special recipes.
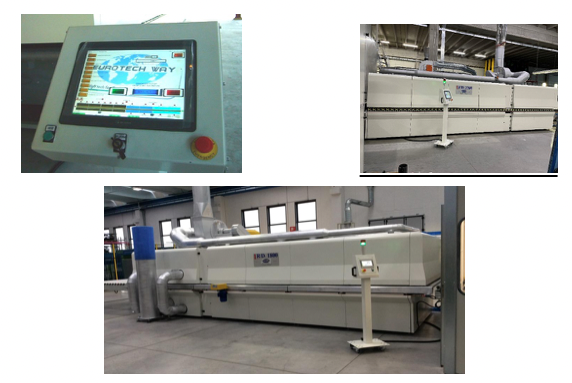
EDGE ROLLING MACHINE
This machine can be equipped with an applicator roller for different glazes and processes.
The head is equipped with devices for manual or automatic glaze feeding, with a closed protective casing for total operator safety.
A new system developed by Eurotech-Way was installed which allows to solve the problem of overlapping of the glaze during the intersection of the edges almost completely.
The roller conveyor is equipped with a lifting bench, which allows the movement and rotation of the glass plates by means of the free spheres mounted on the supports.
Particular attention has been paid to the applicator roller and the dosing roller, as well as to the glaze containment system which allows you to keep the inside of the rollers perfectly clean without damaging them.
The main technical characteristics of the edge rolling machine I'm:
1. ROLLER CONVEYORS
• Automatic glass sheet feeding via motorized roller conveyor equipped with perfectly straight rollers and production speed change via touch-screen operator interface.
• Lifting bench with free spheres, which ensure perfect lifting of the glass, facilitating its handling.
• On the opposite side of the application head, there is a retractable support system for large glass plates, which facilitates handling.
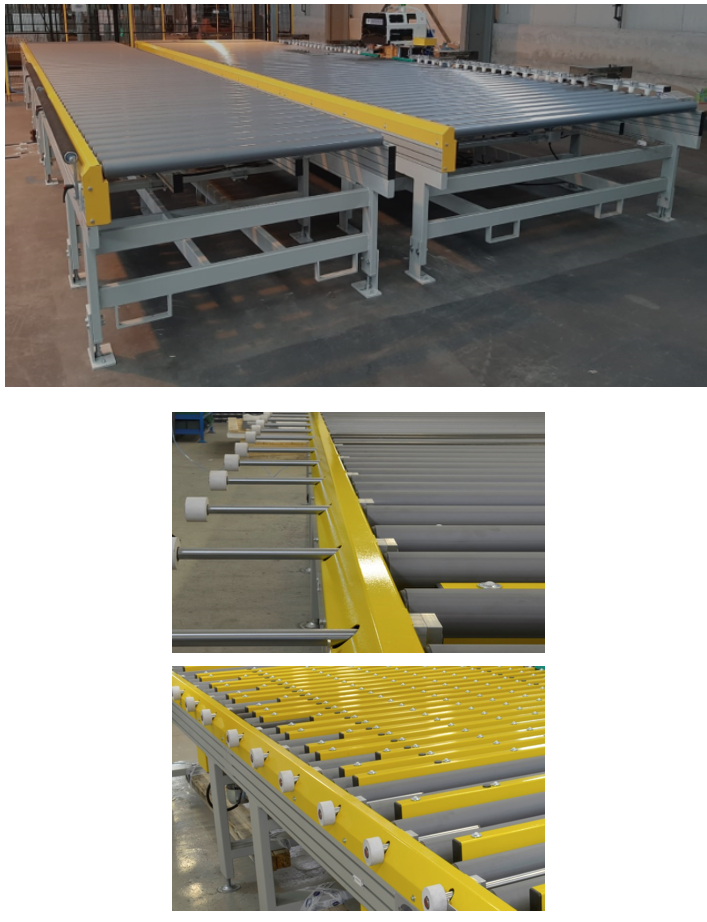
2. AUTOMATIC SUPPORT SYSTEM
Automatic system to determine a precise zeroing point and the width of the edge of the slab to be glazed, programmable via operator interface.
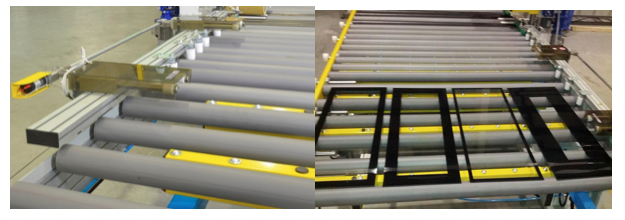
3. ELECTRONIC CONTROL
The machine is equipped with a mobile electronic panel that can be moved from one side of the roller conveyor to the other according to the size of the glasses to facilitate the operator during the machine setting operations. The operator interface is equipped with a touch-screen panel, PLC and dedicated software for memorizing and recalling the processing recipes.
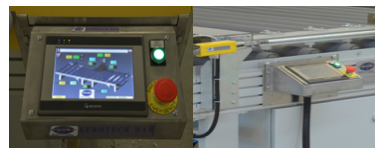
4. ENAMELLED HEAD UNIT
All the glazing head rollers can move in any direction, with decimal adjustments during the work phases. This guarantees:
• Precise adjustment to have a perfect and uniform distribution of the glaze on the applicator roller.
• Precise adjustment of the distance between the applicator roller and the dosing roller, adjustable via touch-screen panel.
• The speeds of both rollers are controlled separately and adjustable via a touch-screen panel and related inverters.
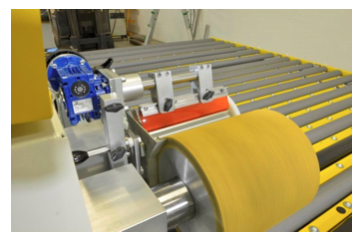
The glazing head unit has been designed so that the glaze can be fed automatically or manually and is equipped with a fully enclosed casing which prevents any possible contact of the rollers with the operator.
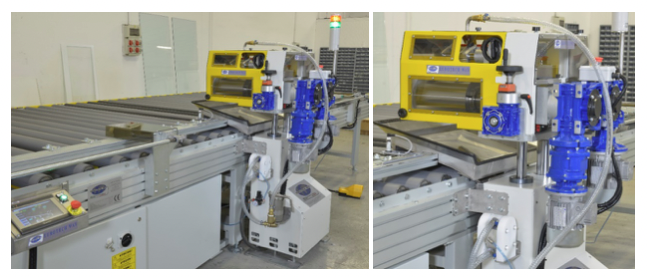
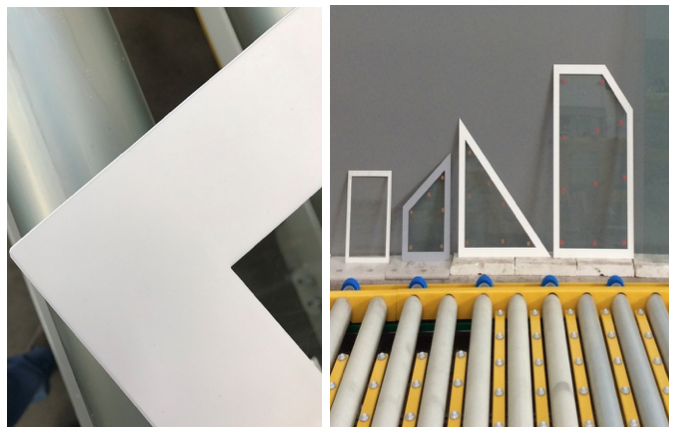