Who has never observed, handled, uncorked a bottle of the popular drink: beer.
But how is a glass bottle born?
It is a very ancient process, which it is evolved to very sophisticated industrial levels, so much so as to elect the glass bottle as the most suitable container to accommodate beer and other fine drinks.
The first phase productive consists in production of molten glass.
Large quantities of glass cullet, derived from separate collection, added to silicon oxide, other vitrifiable substances (such as oxides and anhydrides of boron and phosphorus), which are brought to the melting temperature, variable between 1200-1500 ° C.
This red-hot mass is allowed to cool at about 800 ° C, so that it acquires a sufficient viscosity so as to be workable (or better divided into portions)
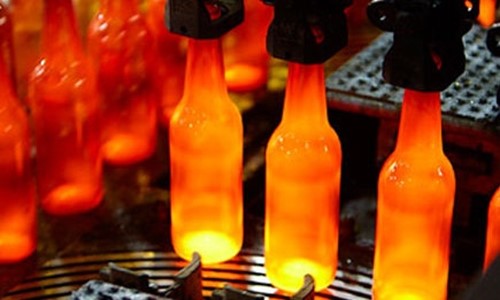
The next steps are dedicated to the shaping of the container and in the case of common beer bottles they can use two techniques alternatives:
La "press-blow" technique: a drop of molten glass is placed in a first mold, in which a first shape of the mouth and of the body is forged thanks to the pressing by a piston; then follows the acquisition of the final structure through a second mold and the insufflation of air.
La "blow-blow" technique: in which the process is always carried out thanks to two molds and with the same sequence, but uses compressed air at about 200 bar.
This is the most widespread industrial technique for small mouth containers, like, precisely the bottles.
The forming machines can process several glass drops at the same time, up to as many as 500 pieces per minute.
The temperature of the glass in the second mold is about 450-500 ° C and therefore there is a very rapid thermal variation.
This situation creates strong structural criticalities of the newborn glass container and it is used to cancel the present tensions to the annealing operation, by heating at about 500 ° C for a few seconds.
On leaving the so-called cold zone (40-60 ° C) all containers have a strict quality control to check for any defects (inclusions, cracks, breaks), the regularity of the shape and the embouchure.
Other checks, such as resistance to internal pressure, volumetric capacity, resistance to thermal shock, are made on a sample basis.
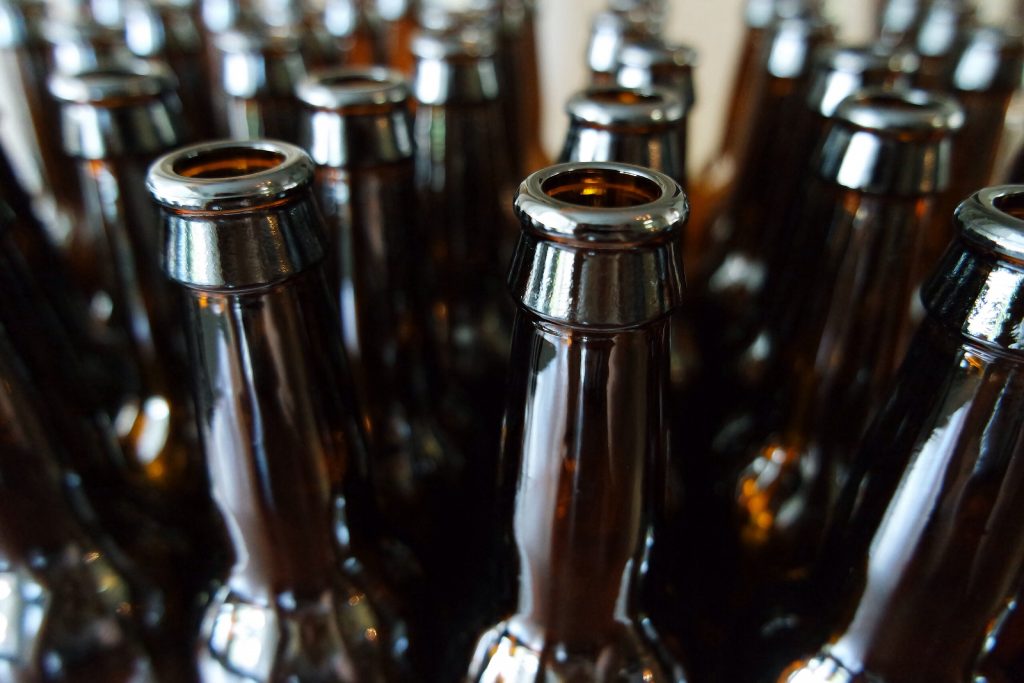
In recent years the production technology has had important evolutions, giving life to ever lighter packaging, but with great mechanical resistance.
These advances have been achieved thanks to the introduction of chemical and thermal strengthening processes or by surface treatments.
With these improvements, the weight of the glass containers has been halved compared to that of 30-40 years ago.
Source: dellabirra.it newspaper