De uitvinding van het floatglasproces
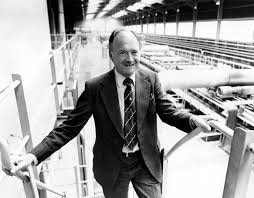
Het proces dat "floatglas" wordt genoemd voor de industriële productie van vlakglas werd eind jaren vijftig geïntroduceerd.
Het was Sir Alastair Pilkington die dit fabricageproces perfectioneerde: hij stelde zichzelf ten doel om tegen lagere kosten het glas te verkrijgen van de kwaliteit die nodig is om autoruiten, spiegels en andere toepassingen te maken waar de afwezigheid van visuele aberraties. Tot dan toe werd de printmethode gebruikt, die erin bestond het vel te maken door middel van gieten, extrusie of lamineren: de oppervlakken hadden dus geen optisch evenwijdige vlakken, wat aanleiding gaf tot de kenmerkende visuele aberraties. Parallelliteit werd vervolgens verkregen door een mechanische polijstbewerking en dit bracht een aanzienlijke kostenstijging met zich mee.
Waarom heet het floatglas?
Het gebruik van de term float, van het Engelse werkwoord “to float” wat “float” betekent, is te wijten aan het feit dat op een bepaald punt in het proces het glaslint in formatie blijkt te drijven op een laag gesmolten tin.
De productiestadia
De fusie
De gebruikte grondstoffen zijn: een verglazingsmiddel - kiezelzand (73%), een stabilisator - calciumcarbonaat (9%), een vloeimiddel - natriumsulfaat (13%). Aan deze componenten wordt een bepaalde massa gerecycled glas toegevoegd, in fragmenten, om het gasverbruik van de smeltovens te verminderen.
De grondstoffen in een silo worden gewogen, gemengd en bevochtigd. Op deze manier wordt een verglaasbaar mengsel verkregen dat via transportbanden naar de smeltoven wordt getransporteerd, waar de temperatuur 1550 ° bereikt.
Het tinnen bad
Bij het verlaten van de oven wordt het gesmolten glas over een bad van vloeibaar tin, het “vlotterbad”, met een temperatuur van ongeveer 1.000 ° C geleid.
Glas, dat bij deze temperatuur erg stroperig is, mengt niet met vloeibaar tin, maar drijft erop en vormt een vlak en glad oppervlak. Het glas wordt dan getrokken om een "lint" te worden met parallelle vlakken. Tandwielen (toprollen) rekken of trekken het glas lateraal in om de gewenste breedte en dikte te verkrijgen (die kan variëren van 1,1 tot 19 mm).
Gloeien
Om ervoor te zorgen dat het glaslint, dat absoluut vlak is gemaakt, zonder problemen in platen kan worden gesneden, is de gloeifase noodzakelijk: het dient om de interne spanningen van het glas te wijzigen.
Het glas verlaat het tinbad met een temperatuur van ongeveer 600 ° C en zet zich neer op de rollen van een koeltunnel (ongeveer 100 meter lang): bij 500 ° C krijgt de glasstrip de eigenschappen van een perfect elastische vaste stof en het blijft gecontroleerd afkoelen tot het op kamertemperatuur is gekomen.
Snijden
De baan is klaar om te worden gesneden in standaard glasplaten (3.210 x 6.000 mm) en de langsranden zijn weggewerkt. Aan het einde van de lijn worden de platen met zuignapliften verplaatst en verticaal op de ruggen gepositioneerd.
Onderstaande figuur laat van links naar rechts zien: de voeding met grondstoffen, de smeltovens, de eerste afkoeling op gesmolten tin, de gloeioven, het snijden van de gietplaten en het vervolgens laden van de platen op de media van vervoer.
