A invenção do processo de vidro float
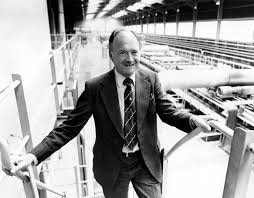
O processo denominado "vidro float" para a produção industrial de vidro plano foi introduzido no final dos anos XNUMX.
Foi Sir Alastair Pilkington quem aperfeiçoou este processo de fabricação: ele se propôs a obter, a custos mais baixos, vidros com a qualidade necessária para fazer vidros, espelhos e outros usos onde a ausência de aberrações visuais. Até então, era utilizado o método de impressão, que consistia na confecção da folha por fundição, extrusão ou laminação: as superfícies, conseqüentemente, não apresentavam faces opticamente paralelas, dando origem às aberrações visuais características. O paralelismo foi posteriormente obtido através de uma operação de polimento mecânico e isso envolveu um aumento considerável de custos.
Por que é chamado de vidro float?
A utilização do termo float, do verbo inglês “to float” que significa “to float”, se deve ao fato de que, em determinado momento do processo, a fita de vidro em formação flutua sobre uma camada de estanho fundido.
As etapas de produção
A fusão
As matérias-primas utilizadas são: um agente vitrificante - areia de sílica (73%), um estabilizador - carbonato de cálcio (9%), um fundente - sulfato de sódio (13%). A esses componentes é adicionada uma certa massa de vidro reciclado, em fragmentos, para reduzir o consumo de gás dos fornos de fundição.
As matérias-primas contidas em um silos são pesadas, misturadas e umidificadas. Obtém-se assim uma mistura vitrificável que é transportada por correias transportadoras para o forno de fusão, onde a temperatura atinge 1550 °.
O banho de estanho
Ao sair do forno, o vidro fundido é passado por um banho de estanho líquido, o “banho de flutuação”, a uma temperatura de cerca de 1.000 ° C.
O vidro, que é muito viscoso a esta temperatura, não se mistura com o estanho, que é fluido, mas flutua sobre ele formando uma superfície plana e lisa. O vidro é então puxado para se tornar uma "fita" com faces paralelas. As rodas dentadas (rolos superiores) esticam ou retraem o vidro lateralmente para obter a largura e a espessura desejadas (que pode variar de 1,1 a 19 mm).
anelamento
Para que a fita de vidro, feita absolutamente plana, seja cortada em lâminas sem problemas, é necessária a fase de recozimento: serve para modificar as tensões internas do vidro.
O vidro sai do banho de estanho a uma temperatura de cerca de 600 ° C e é depositado nos rolos de um túnel de resfriamento (cerca de 100 metros de comprimento): a 500 ° C a tira de vidro adquire as propriedades de um sólido perfeitamente elástico e então ele continua a esfriar sob controle até atingir a temperatura ambiente.
Corte
A banda está pronta para ser cortada em folhas de vidro padrão (3.210 x 6.000 mm) e as bordas longitudinais são eliminadas. No final da linha as lajes são movidas com elevadores de ventosas e posicionadas verticalmente nas costas.
A figura abaixo ilustra, da esquerda para a direita: a alimentação com matéria-prima, os fornos de fusão, o primeiro resfriamento em estanho fundido, o forno de recozimento, o corte das placas de fundição e o subsequente carregamento das placas no meio. do transporte.
