Sự phát minh ra quy trình kính nổi
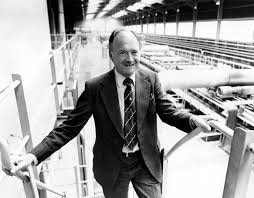
Quy trình được gọi là "kính nổi" để sản xuất công nghiệp kính phẳng đã được giới thiệu vào cuối những năm XNUMX.
Chính Ngài Alastair Pilkington là người đã hoàn thiện quy trình sản xuất này: ông ấy đặt cho mình mục tiêu là có được, với chi phí thấp hơn, loại kính có chất lượng cần thiết để làm kính ô tô, gương và các mục đích sử dụng khác khi không có quang sai thị giác. Cho đến lúc đó, phương pháp in được sử dụng, bao gồm việc tạo ra tấm bằng cách đúc, đùn hoặc cán: các bề mặt, do đó, không có các mặt song song về mặt quang học, làm phát sinh quang sai hình ảnh đặc trưng. Sự song song sau đó đã đạt được thông qua hoạt động đánh bóng cơ học và điều này làm tăng chi phí đáng kể.
Tại sao nó được gọi là kính nổi?
Việc sử dụng thuật ngữ float, từ động từ tiếng Anh “to float” có nghĩa là “nổi”, là do thực tế là tại một thời điểm nhất định trong quá trình này, dải băng thủy tinh trong quá trình hình thành được tìm thấy nổi trên một lớp thiếc nóng chảy.
Các giai đoạn sản xuất
Sự hợp nhất
Các nguyên liệu thô được sử dụng là: chất thủy tinh hóa - cát silica (73%), chất ổn định - canxi cacbonat (9%), chất trợ dung - natri sunphat (13%). Đối với những thành phần này, một lượng thủy tinh tái chế nhất định được thêm vào, ở dạng mảnh, để giảm tiêu thụ khí đốt của các lò luyện.
Nguyên liệu thô chứa trong silo được cân, trộn và làm ẩm. Bằng cách này, một hỗn hợp có thể trộn được sẽ thu được bằng băng tải đến lò nung chảy, ở đó nhiệt độ đạt tới 1550 °.
Bồn tắm bằng thiếc
Khi rời khỏi lò nung, thủy tinh nóng chảy được đưa qua bể thiếc lỏng, "bể nổi", ở nhiệt độ khoảng 1.000 ° C.
Thủy tinh, rất nhớt ở nhiệt độ này, không trộn lẫn với thiếc là chất lỏng, mà nổi lên trên nó tạo thành một bề mặt phẳng và nhẵn. Sau đó, kính được kéo để trở thành một "dải băng" với các mặt song song. Bánh răng (cuộn trên) kéo căng hoặc thu lại kính theo chiều ngang để có được chiều rộng và độ dày mong muốn (có thể thay đổi từ 1,1 đến 19 mm).
Ủ
Để dải băng thủy tinh, được làm phẳng tuyệt đối, có thể cắt thành các tấm mà không gặp vấn đề gì, giai đoạn ủ là cần thiết: nó phục vụ cho việc điều chỉnh lực căng bên trong của kính.
Thủy tinh rời khỏi bể thiếc ở nhiệt độ khoảng 600 ° C và được lắng đọng trên các con lăn của đường hầm làm mát (dài khoảng 100 mét): ở 500 ° C, dải thủy tinh có được các đặc tính của một chất rắn đàn hồi hoàn hảo và sau đó nó tiếp tục làm mát trong tầm kiểm soát cho đến khi nó đạt đến nhiệt độ phòng.
Cắt
Web đã sẵn sàng được cắt thành các tấm kính tiêu chuẩn (3.210 x 6.000 mm) và các cạnh dọc được loại bỏ. Ở cuối dây chuyền, các tấm được di chuyển bằng thang máy hút và định vị thẳng đứng ở mặt sau.
Hình dưới đây minh họa, từ trái sang phải: thức ăn với nguyên liệu thô, lò nung chảy, lần làm nguội đầu tiên trên thiếc nóng chảy, lò ủ, cắt các tấm đúc và việc nạp các tấm tiếp theo lên phương tiện. của phương tiện giao thông.
